Written By: Dan Blondal, CEO, Director & Founder, Nano One Materials Corp.
The overlooked chokepoint threatening to stall the world’s energy and defence ambitions.
As global trade systems are up-ended, supply chains rethought, and energy security reprioritized, it is easy to dismiss the relevance of lithium-ion batteries. We think they’re central.
Beyond their role in a low-carbon economy, the low-cost, high-quality advantage of Chinese EVs is a direct competitive threat to the future of Western automakers. Batteries are also the foundation of energy storage systems (ESS) and have become central to energy security and sovereignty. That’s why batteries are no longer just a clean tech story—they’re a strategic asset.
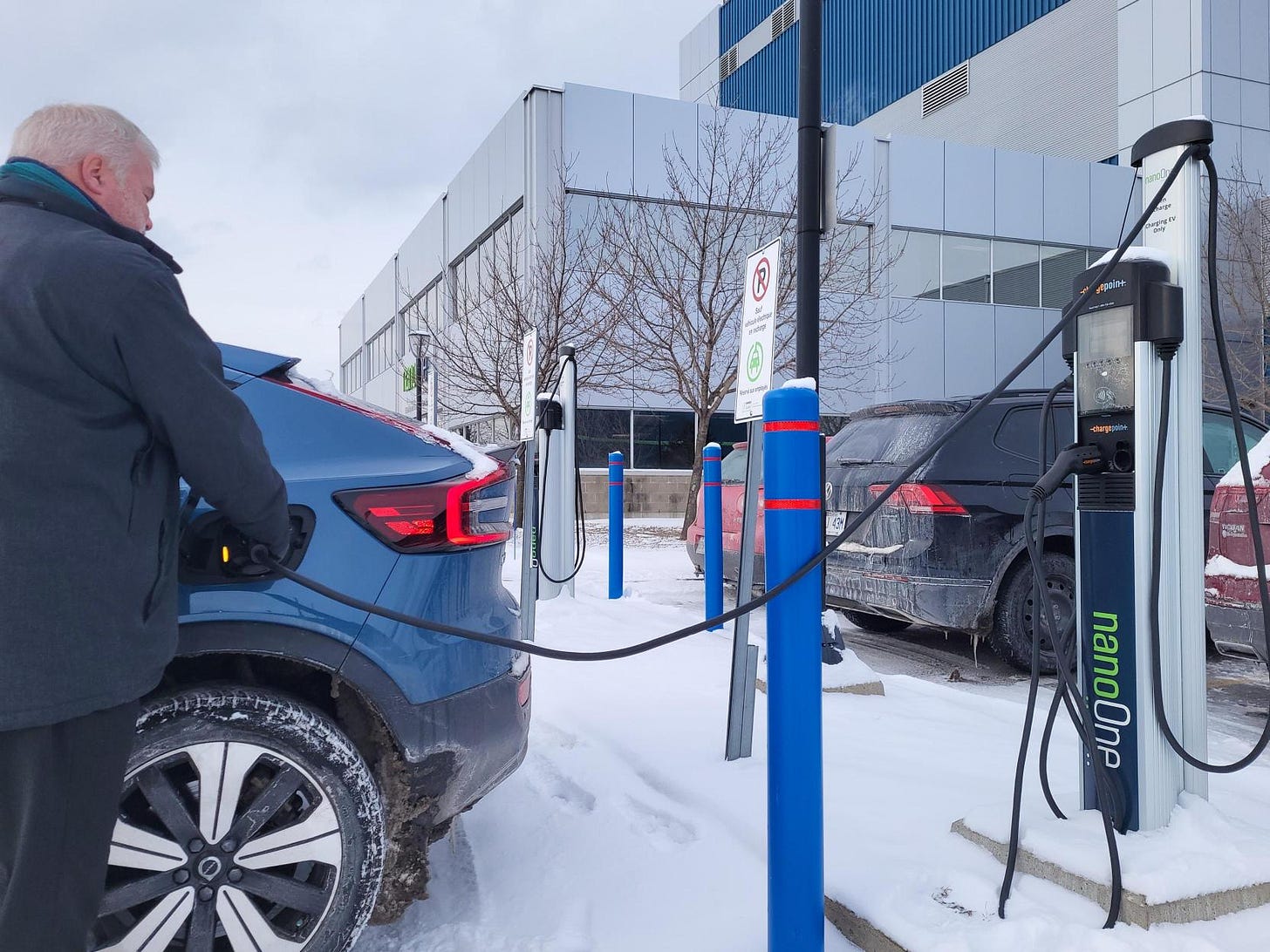
From electric military vehicles to grid-scale storage and AI-driven defence systems, batteries underpin modern logistics and operations. Governments are responding by ramping up defence spending, catalyzing supply chains, and rethinking the industries that enable them. But there’s also a clear role for automakers here—not just to catch up but to embrace the future and lead what comes next.
The push to localize battery production and secure the critical minerals needed has already begun. But that’s not enough. The real bottleneck is what happens after extraction—how we refine, process, and transform them into cost-competitive cathode materials, at scale and at home.
Cathode materials account for 30–50% of a lithium-ion battery’s total cost, and their production is notoriously difficult to localize. Production is costly, hard to permit, and tied to overseas manufacturing and proprietary know-how.
China controls the metal-sulfate inputs, using capital-, water-, and energy-intensive methods that are challenging to replicate and permit in North America, Europe, and other emerging battery markets. Attempts to copy and paste this model in the West have consistently failed.
There has to be a better way.
Nano One’s One-Pot™ Processing Technology
We’ve been thinking differently from the start.
A decade ago, my team and I focused in on this problem. We believe that changing cathode production—economically, locally, and at scale—is the key to differentiating and controlling battery supply chains. Through sustained R&D, we developed a new approach that reduces cost and complexity, eliminates waste, and breaks the dependency on foreign-controlled supply chains.
We call it the One-Pot™ process.
One-Pot™ is a platform technology that integrates precursor (pCAM) and cathode (CAM) production into one streamlined process, using domestically sourced metal powders and lithium carbonate as inputs.
The benefits:
- No wastewater—no costly treatment or discharge
- No sodium sulfate by-products—no disposal logistics
- No China-controlled inputs—no exposure to trade uncertainty
- Reduced cost, energy, water, permitting, and supply chain risk
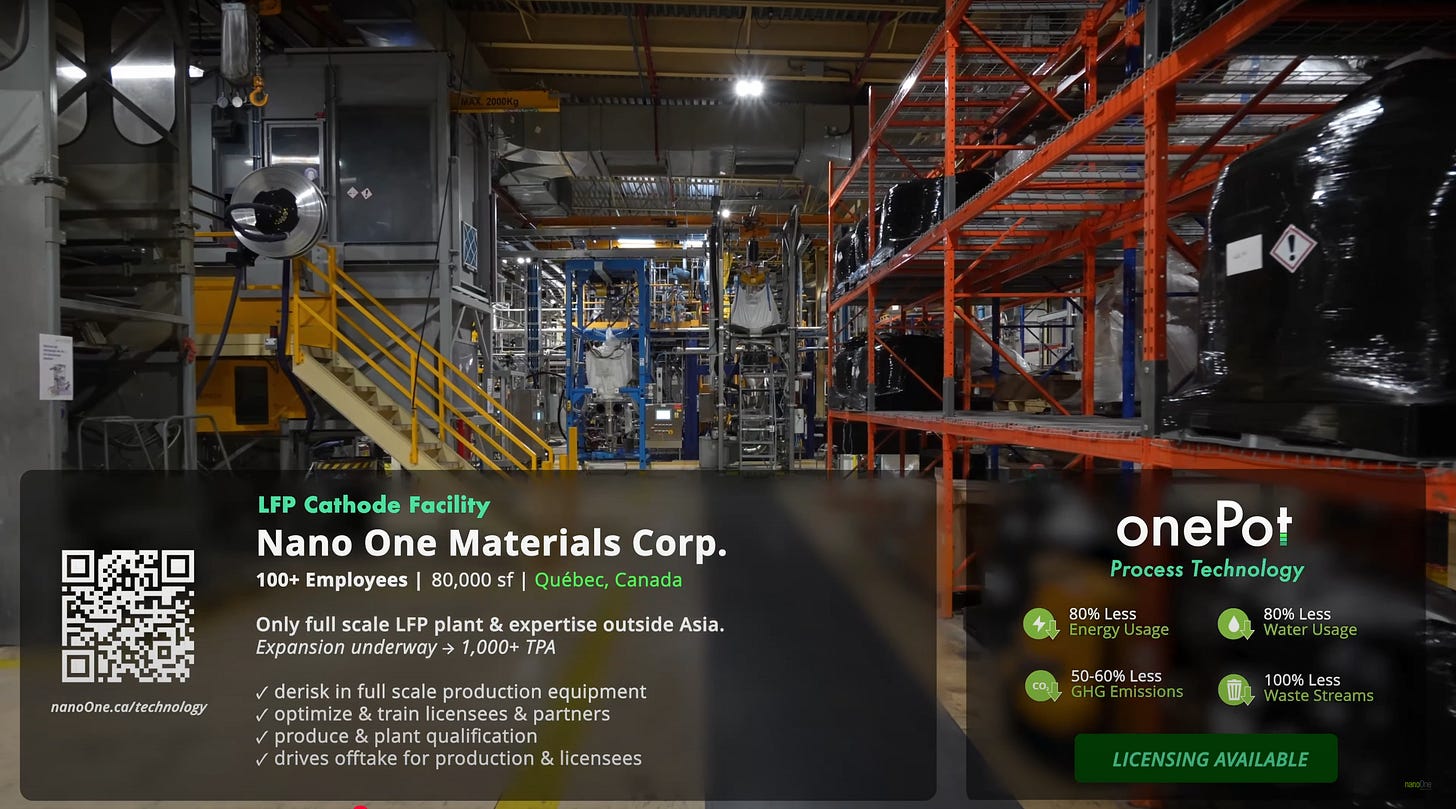
This isn’t theoretical—our Québec facility is North America’s only LFP demonstration plant. It’s operated by a world-class team using full-scale commercial equipment—and it’s already serving as a platform for partnerships, training, and scale-up.
From Pilot to High-Volume Production
We’ve taken a practical, modular approach to scaling. It reduces capital cost, execution risk, and time to deployment.
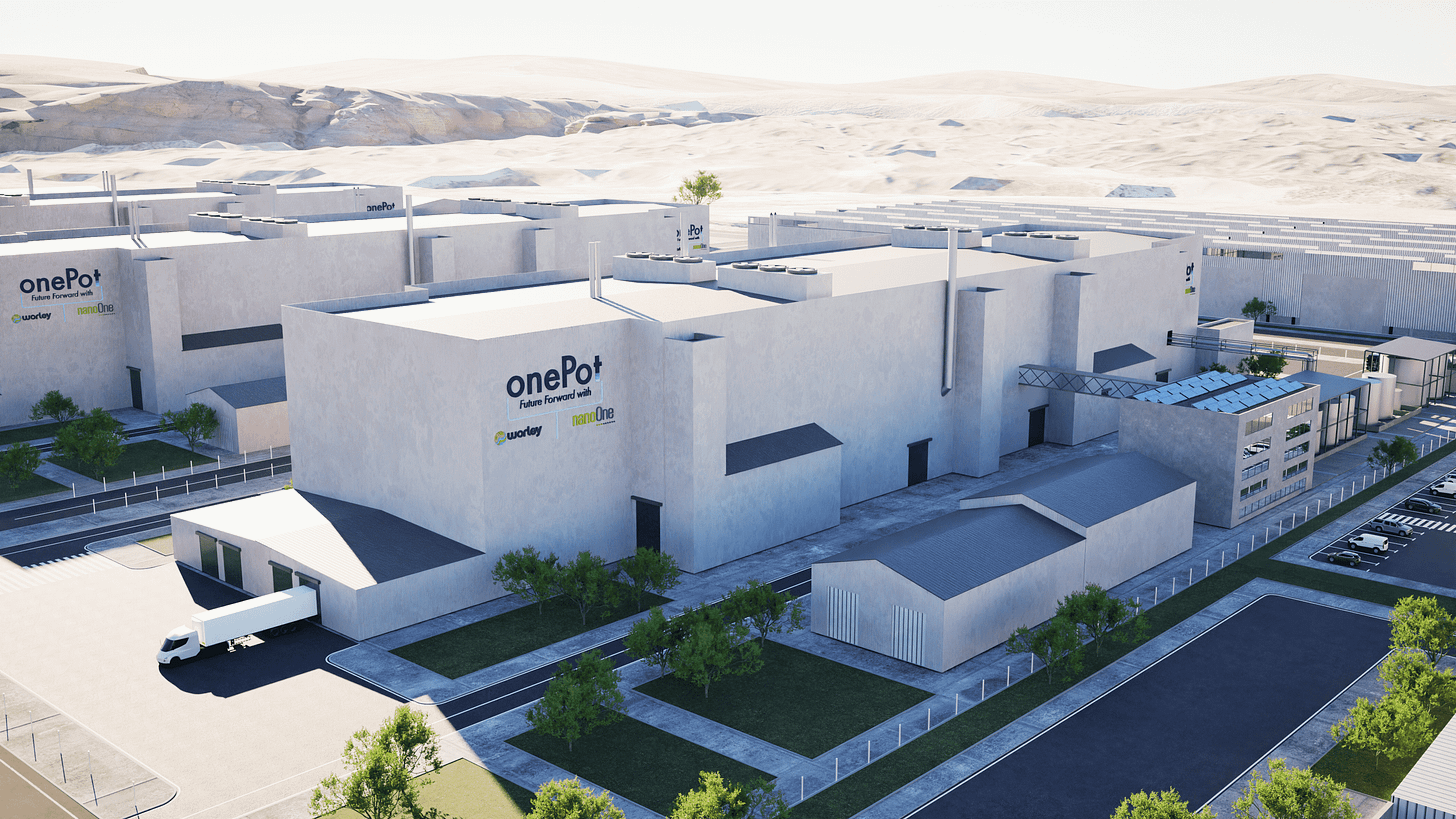
- Our demonstration plant in Québec is a launchpad for revenue and growth
- Our modular strategy reduces engineering timelines and investment risk
- Our Design-One-Build-Many growth strategy enables scalable replication
- Our alliance with Worley provides global reach and delivery capability
- Our platform enables domestic supply chains that enhance energy security
Licensing for Global Impact
Nano One’s Design-One-Build-Many licensing model isn’t just a business strategy—it’s a framework to:
- Disrupt outdated, sulfate-based processes
- Friend-shore battery production through domestic and allied partnerships
- Secure the supply chain with scalable, easier-to-permit technology that reduces reliance on foreign-controlled inputs
As the race to localize battery production intensifies, the winners won’t be defined by mineral access, finance, and infrastructure alone. That is not enough to compete.
Winners will not change the supply chain without process innovation, licensing, widescale adoption, and an ecosystem of partners collaborating on a better future.
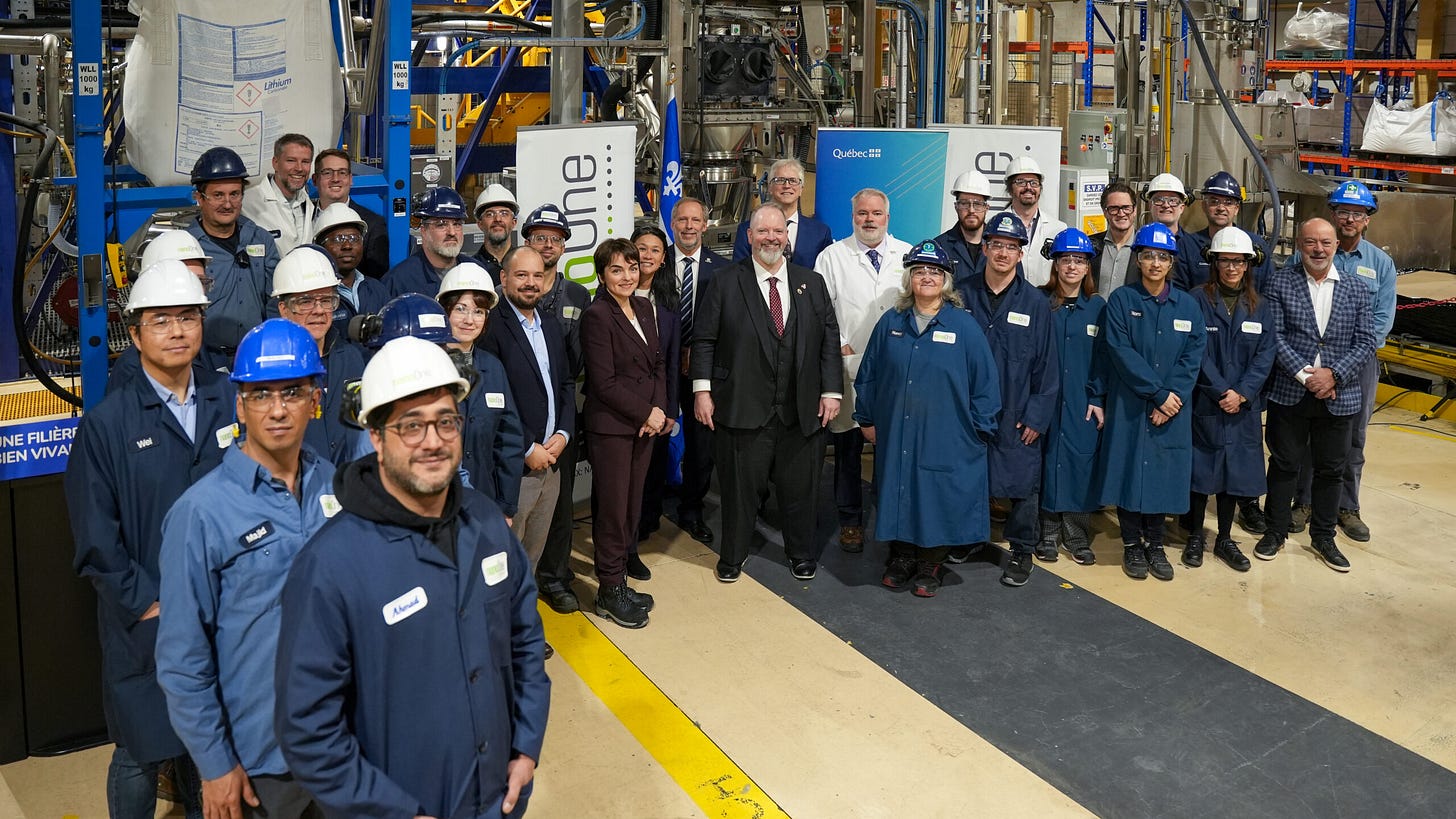
Nano One already has the backing of Sumitomo Metal Mining, Rio Tinto, Worley, the U.S. Department of Defense, and the governments of Canada and Québec.
As the saying goes: It takes a village to raise a child. We think it takes all participants in an ecosystem to scale a better battery supply chain.