Our patented process innovations unlock efficiencies throughout the process, drastically reducing production time, cost and environmental footprint.
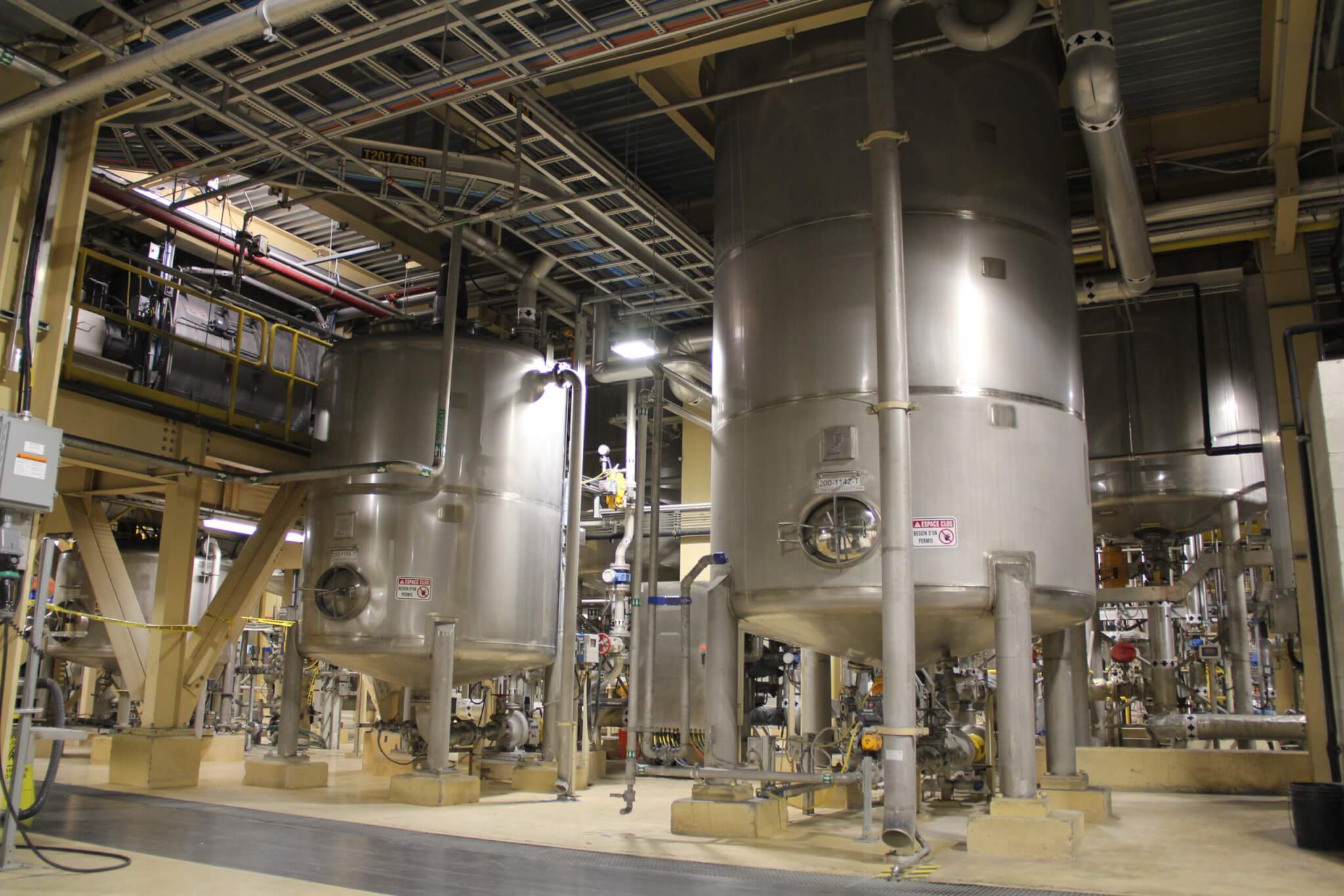
Revolutionizing Cathode Production
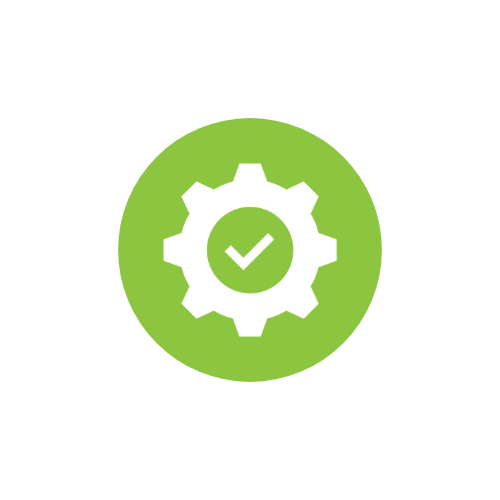
Easier to Permit
Our sulfate-free process eliminates wastewater discharge and cuts GHGs by 50-60%.
Water Usage
We use approximately 80% less water in our production process.
Energy Consumption
Our streamlined One-Pot production unlocks efficiencies through-out the manufacturing process.
Securing the Future of Battery Materials
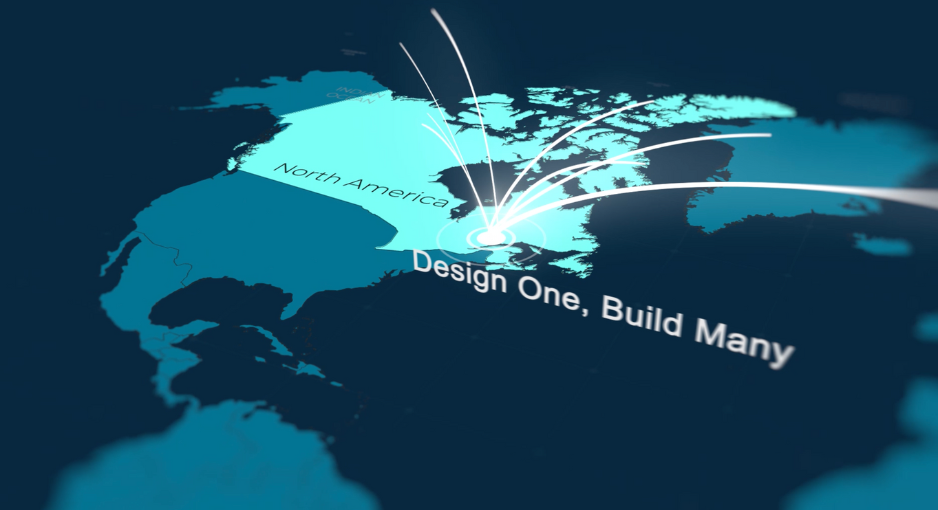
Strengthening Domestic Supply Chains
Our technology reduces permitting hurdles, costs, and reliance on foreign-controlled technology and critical minerals, offering licensable process innovations to enable localized production.
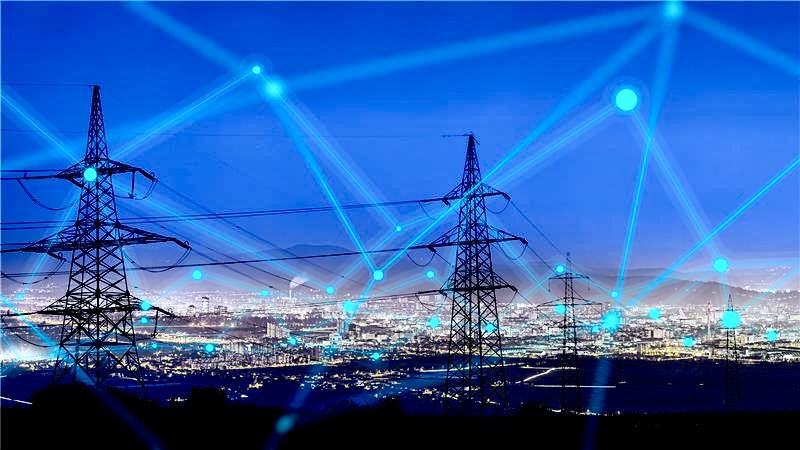
Building Energy Security & Independence
A resilient battery materials supply chain is essential for energy independence. Our process supports self-sufficient, scalable production for EVs, ESS, defense, aerospace, and consumer electronics.
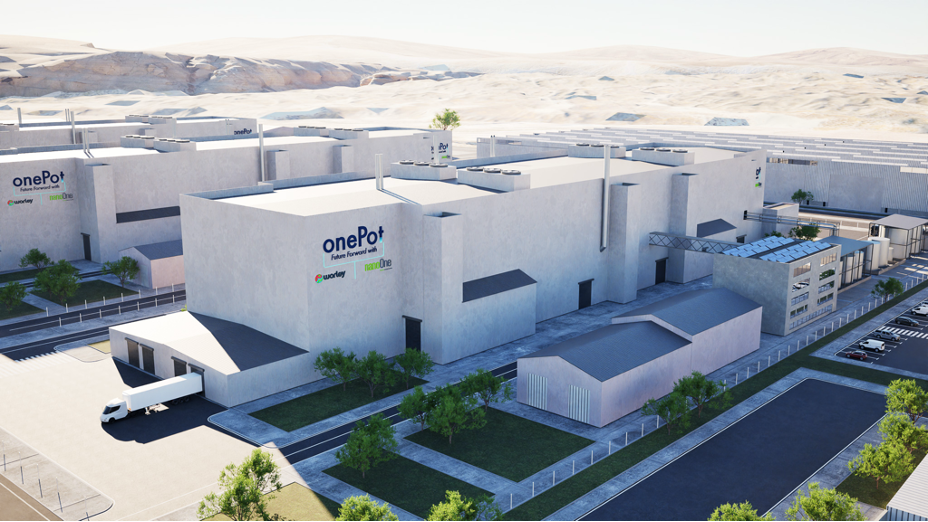
Accelerating Industrial Growth
Investment in battery manufacturing creates jobs, strengthens economies, and reduces supply chain risk. Our streamlined approach lowers permitting barriers, accelerates deployment, and cuts costs for large-scale production.
Nano One’s Innovative Process Solutions
Sulfate-Free Inputs
Our M2CAM® Technology enables sulfate-free metal powder inputs which eliminates 100% of wasteful sodium sulfate by-products while simplifying manufacturing. This innovation also unlocks flexible supply chains for increased security and resiliency.
Streamlined One-Pot Process
Central to our cathode manufacturing solutions, the One-Pot process simplifies production and enables our M2CAM® technology. Our production methods require less water and consume less energy, reducing operational cost and time while using sustainable, scalable design.
Next-Gen Durable Cathodes
Our simplified One-Pot process enables cathodes to form simultaneously with their protective coating at the nano level. This eliminates process steps and protects cathodes from degradation, enhancing durability for a longer-lasting lithium-ion battery.
Compare Production Processes
PCAM

Dissolve into Sulfates
Metals are chemically transformed into metal sulfates in preparation for PCAM process.
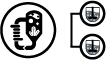
Crystallize / Co-Locate
Crystallize into powders (5-10x heavier) and ship to PCAM producer. Or co-locate with PCAM to avoid crystallization (limited options and flexibility).
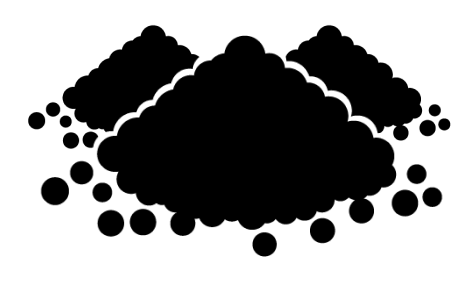
Process into PCAM
Dissolve into PCAM powders, leaving sulfate in solution (1-5x the product stream) with trace metals and water.

Treat Wastewater & Dispose Sulfates
Uses energy and generates large volumes of sulfate, some repurposed, but mostly discharged into waterways where permitting allows.
PCAM
Sulfate-Free Inputs
Our M2CAM® process enables Metals to be transformed directly into Cathode Active Material eliminating many costly and wasteful steps.

Dissolve into Sulfates
Metals are chemically transformed into metal sulfates in preparation for PCAM process.
--
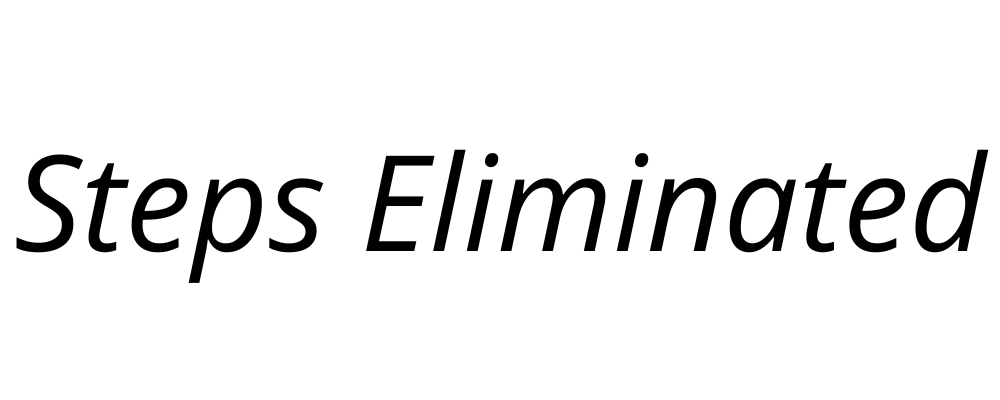
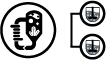
Crystallize / Co-Locate
Crystallize into powders (5-10x heavier) and ship to PCAM producer. Or co-locate with PCAM to avoid crystallization (limited options and flexibility).
--
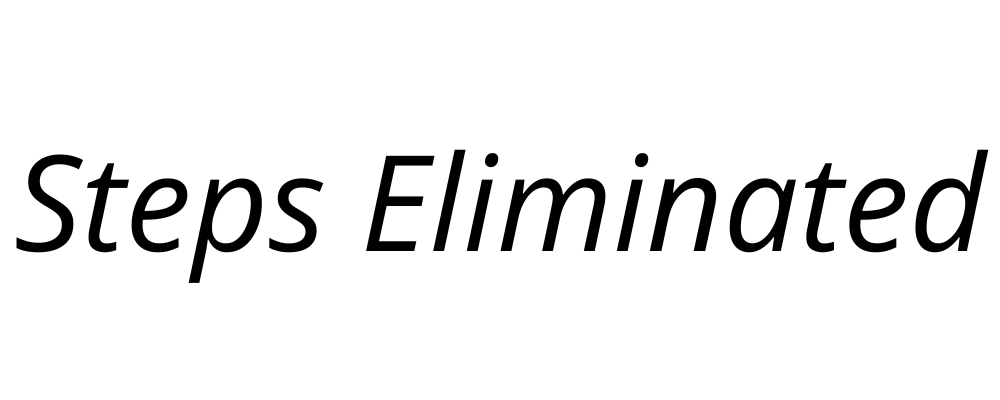
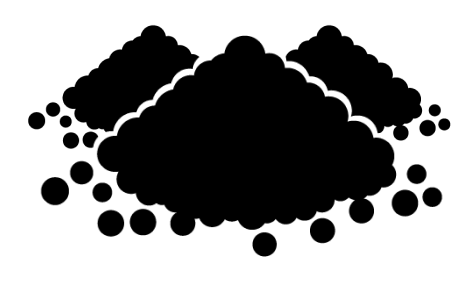
Process into PCAM
Dissolve into PCAM powders, leaving sulfate in solution (1-5x the product stream) with trace metals and water.
--
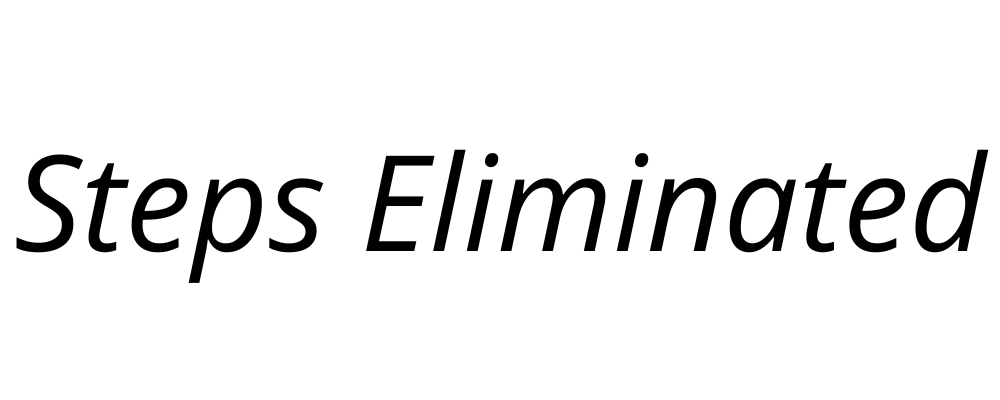

Treat Wastewater & Dispose Sulfates
Uses energy and generates large volumes of sulfate, some repurposed, but mostly discharged into waterways where permitting allows.
--
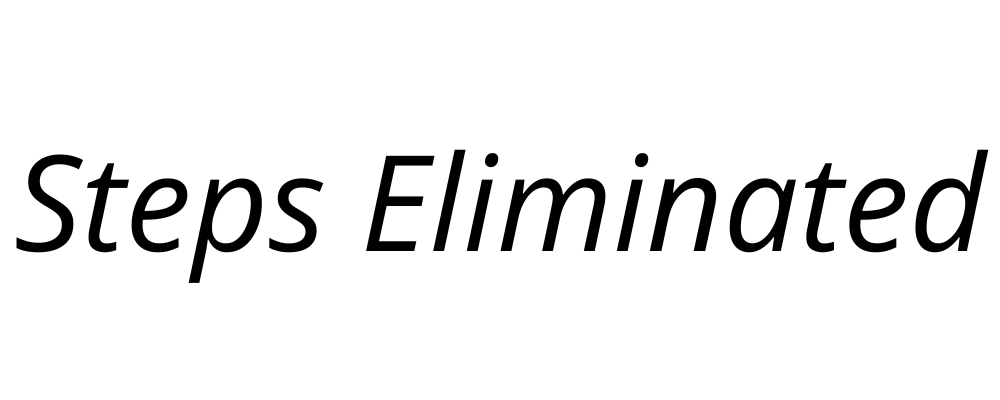
PCAM
Metal-Sulfate Inputs
Requires intermediate chemical transformations that add cost, energy, GHGs and harmful by-products.

Dissolve into Sulfates
Metals are chemically transformed into metal sulfates in preparation for PCAM process.
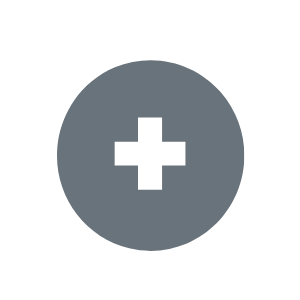
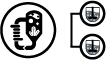
Crystallize / Co-Locate
Crystallize into powders (5-10x heavier) and ship to PCAM producer. Or co-locate with PCAM to avoid crystallization (limited options and flexibility).
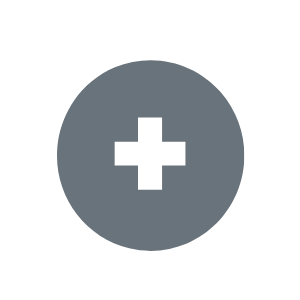
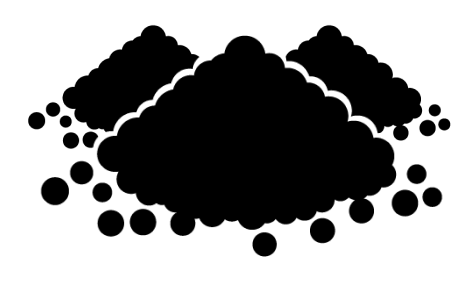
Process into PCAM
Dissolve into PCAM powders, leaving sulfate in solution (1-5x the product stream) with trace metals and water.
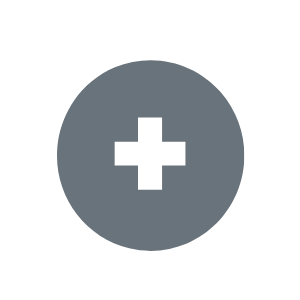

Treat Wastewater & Dispose Sulfates
Uses energy and generates large volumes of sulfate, some repurposed, but mostly discharged into waterways where permitting allows.
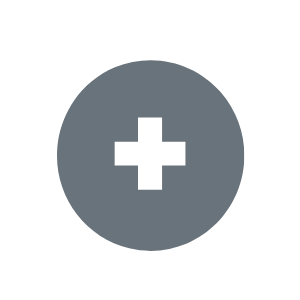
CAM
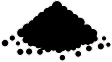
Add Lithium
Lithium is added to the other battery metals.

Process
Lithium mixed metal powder is ground, milled and magnetically separated for contaminants.
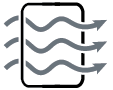
Dry
Lithium mixed metal powder is filtered or spray dried.

Fire in a Kiln
Lithium mixed metal powder is thermally processed at high temperature.

Grind / Mill (Again)
Mill chunky output into powder.

Fire (Again)
Thermally process again.
CAM
Streamlined One-Pot Process
Central to our cathode manufacturing solutions, the One-Pot process simplifies production and enables our M2CAM® technology. Our production methods require less water and consume less energy, reducing operational cost and time while using sustainable, scalable design.
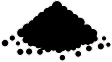
Add Lithium
Lithium is added to the other battery metals.
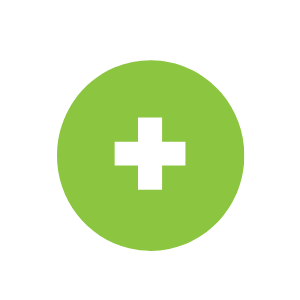

Process
Lithium mixed metal powder is ground, milled and magnetically separated for contaminants.
--
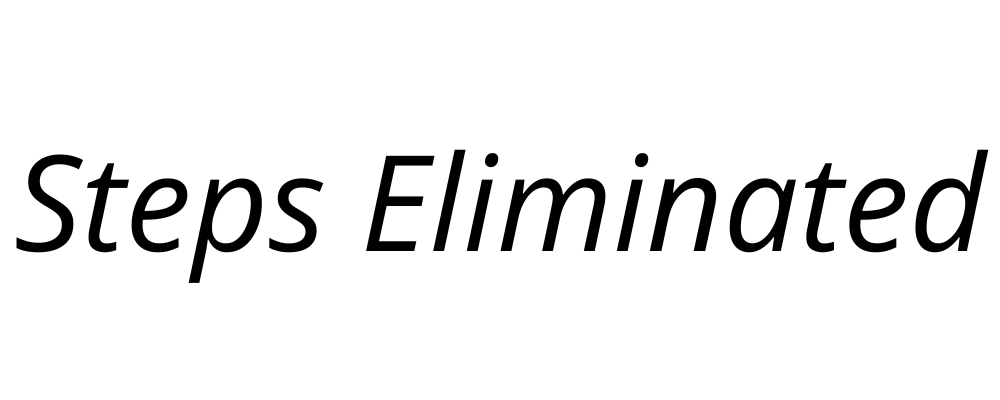
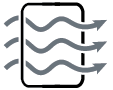
Dry
Lithium mixed metal powder is filtered or spray dried.
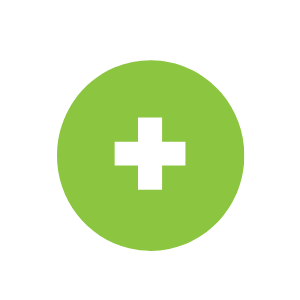

Fire in a Kiln
Lithium mixed metal powder is thermally processed at high temperature.
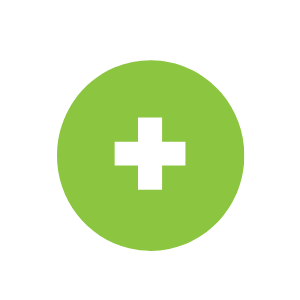

Grind / Mill (Again)
Mill chunky output into powder.
--
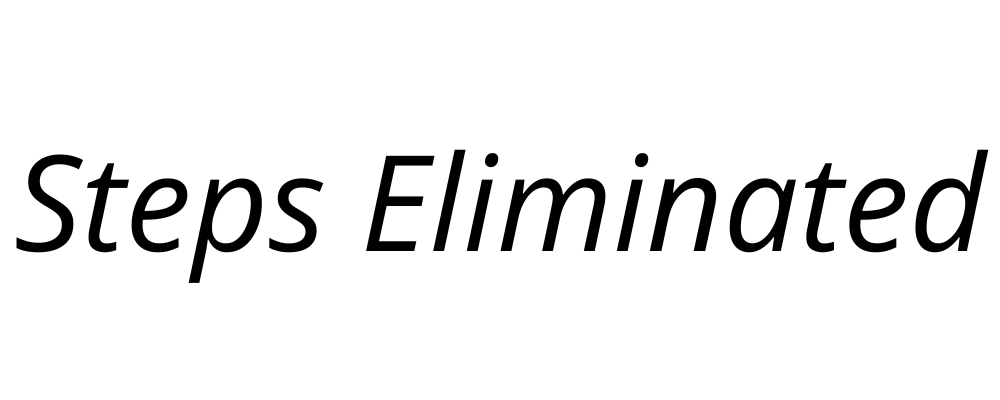

Fire (Again)
Thermally process again.
--
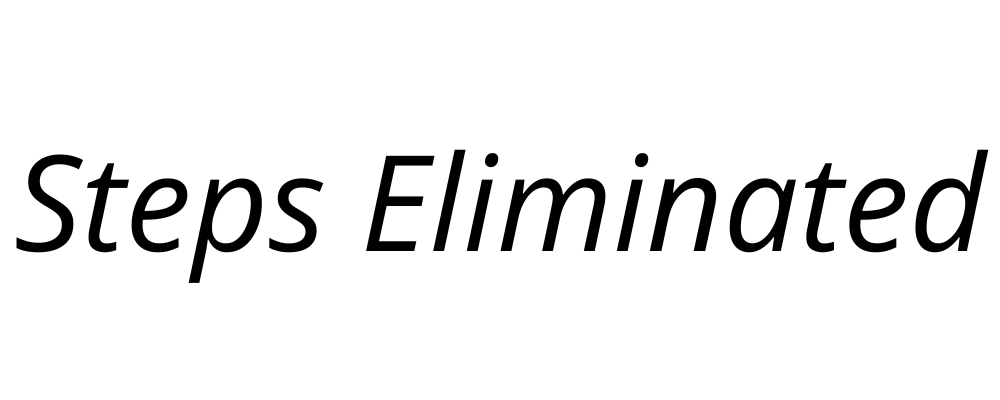
CAM
Energy-Intensive Inefficient Process
The lithiation firing step is long, spanning from hours to days, and energy- intensive. Large, inefficient kilns are used to complete this step which drives up capital and operating expenditures, while presenting scaling challenges.
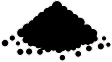
Add Lithium
Lithium is added to the other battery metals.
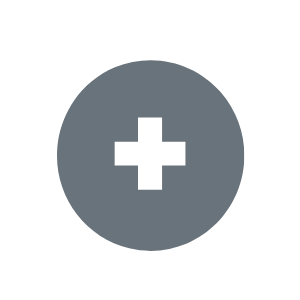

Process
Lithium mixed metal powder is ground, milled and magnetically separated for contaminants.
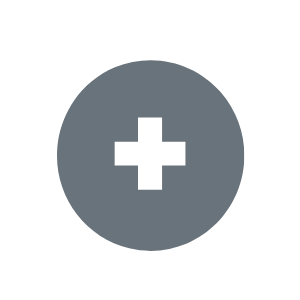
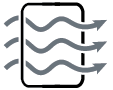
Dry
Lithium mixed metal powder is filtered or spray dried.
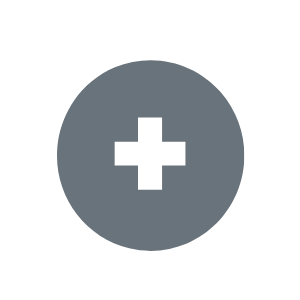

Fire in a Kiln
Lithium mixed metal powder is thermally processed at high temperature.
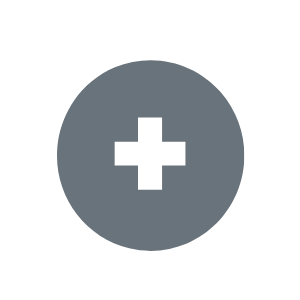

Grind / Mill (Again)
Mill chunky output into powder.
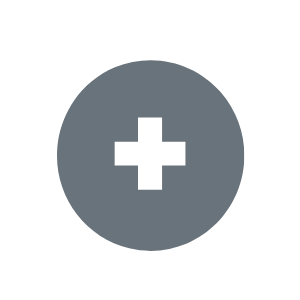

Fire (Again)
Thermally process again.
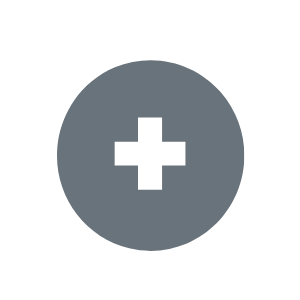
Coated CAM
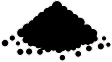
Add Coating
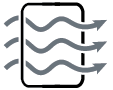
Dry

Fire
Coated CAM
Coated Single Crystal
Protective coatings form simultaneously with CAM, eliminating the need for additional coating steps.
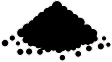
Add Coating
--
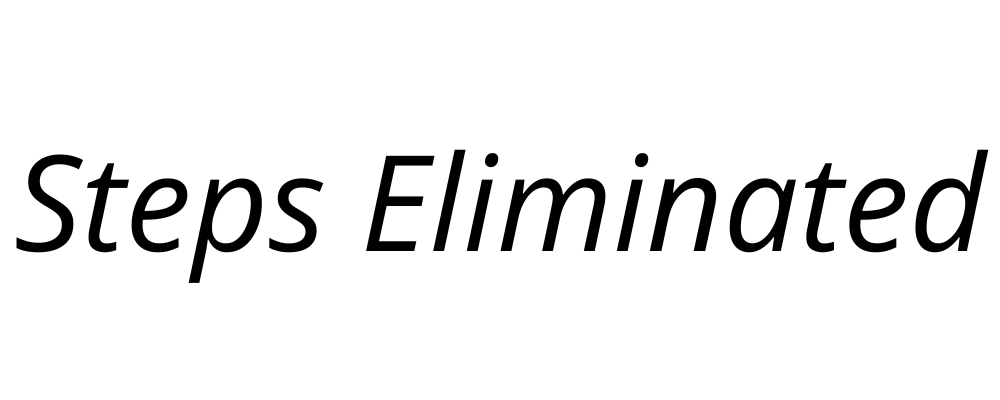
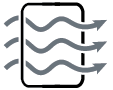
Dry
--
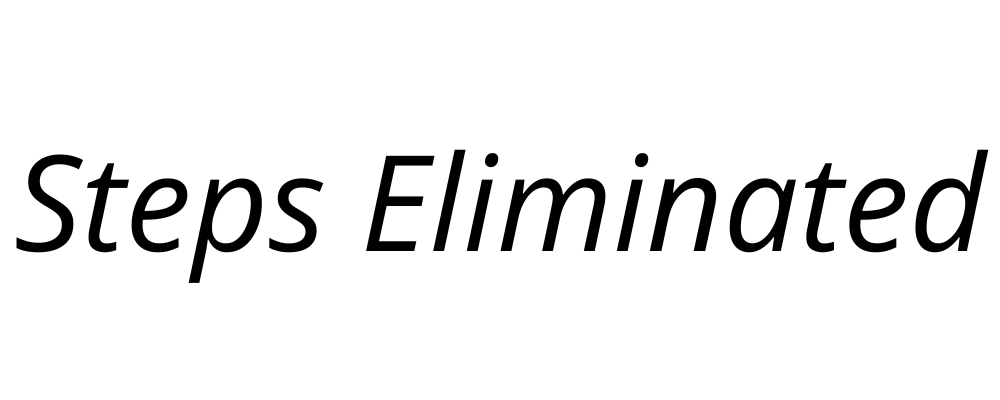

Fire
--
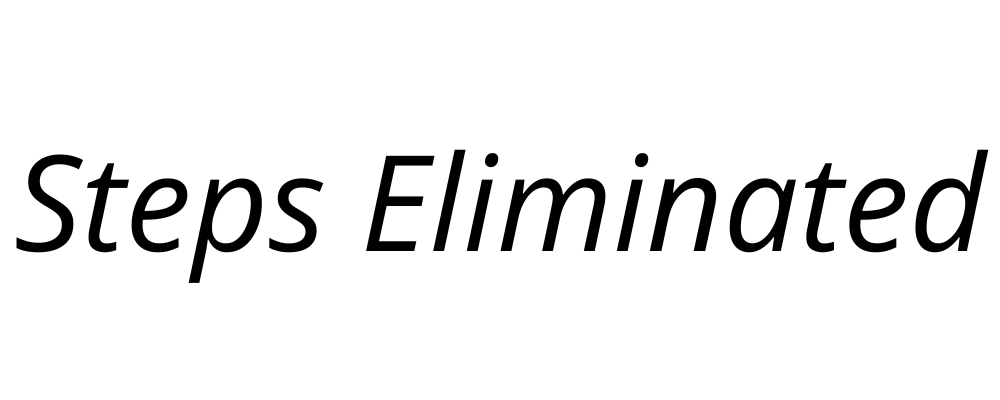
Coated CAM
Coating Adds Steps and Cost
NMC coatings are applied after CAM formation, adding extra steps, costs and energy.
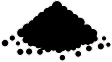
Add Coating
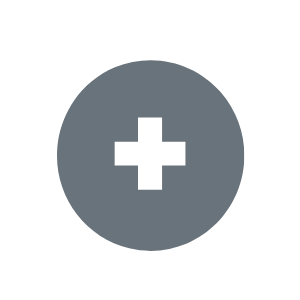
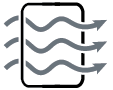
Dry
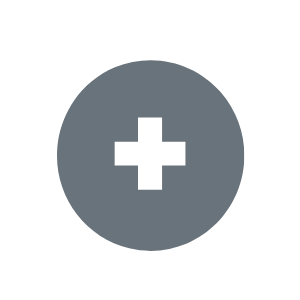

Fire
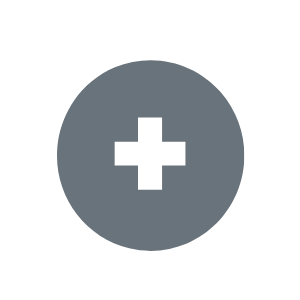
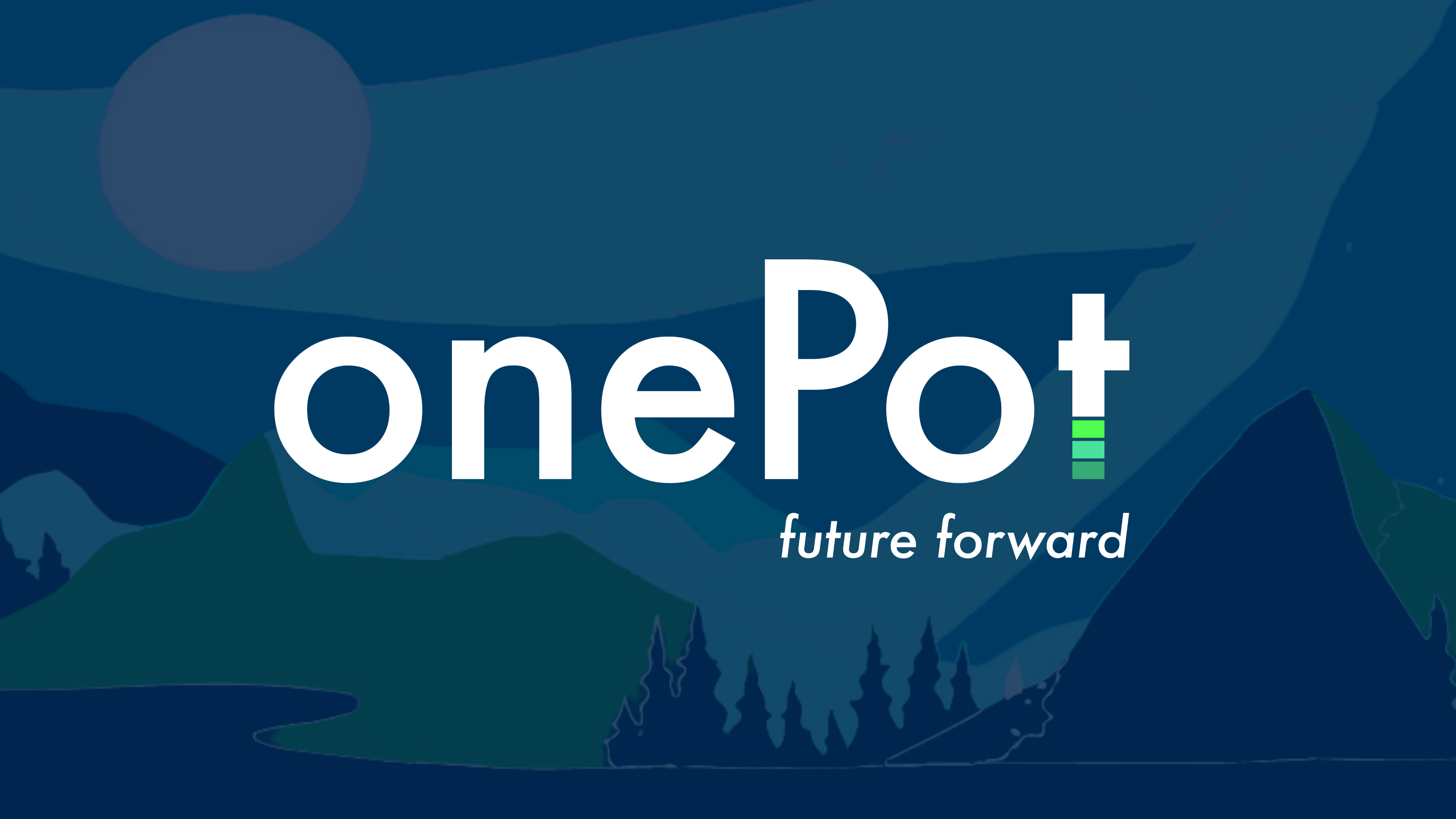
One-Pot™ Process
Our Patented One-Pot™ Process eliminates costly waste treatments, cuts energy use with high-efficiency kilns, and reduces supply chain risk by enabling metal-based feedstocks.
Solving Tomorrow’s Problems, Today
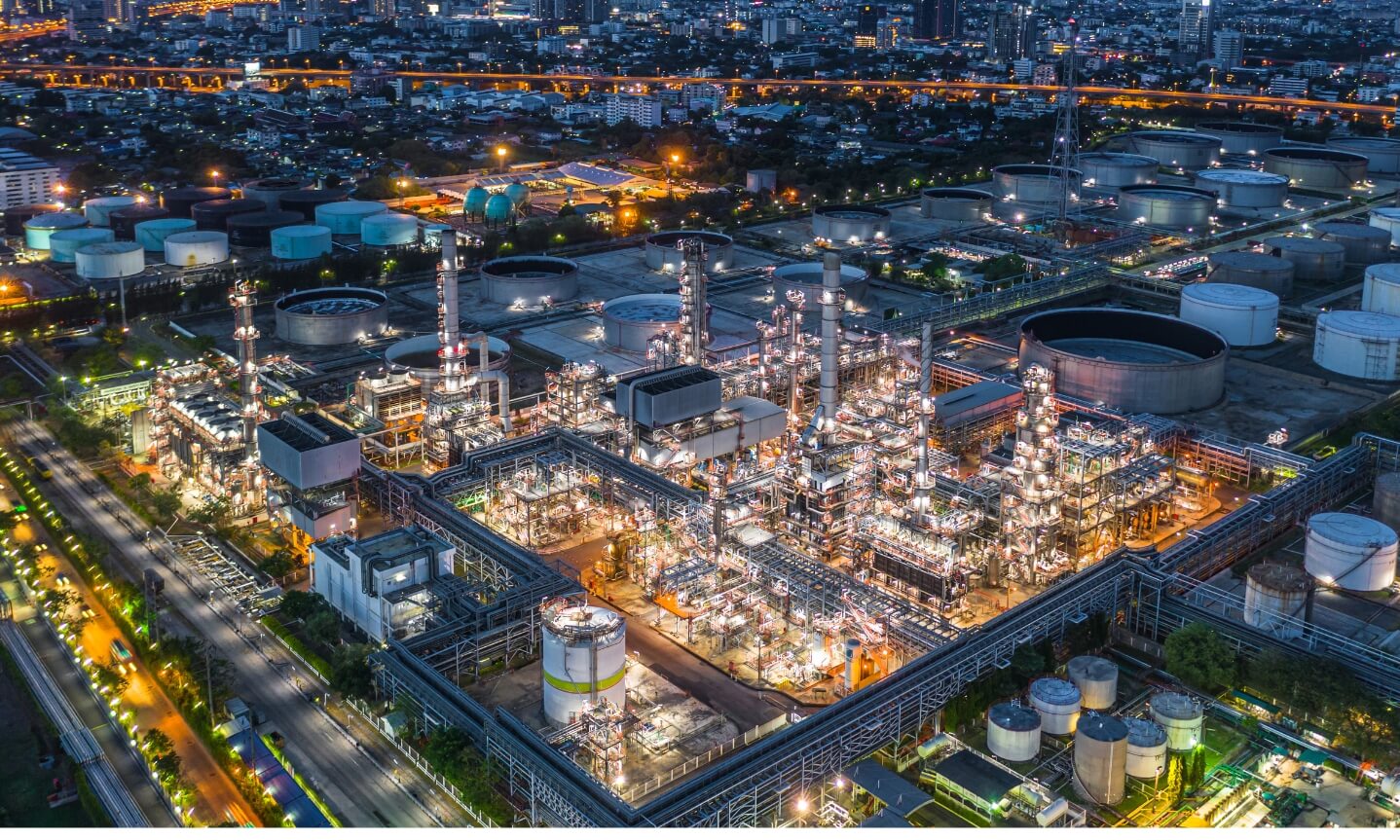
Incumbent processes are energy-intensive and wasteful. When scaled to meet global demand, it becomes untenable.
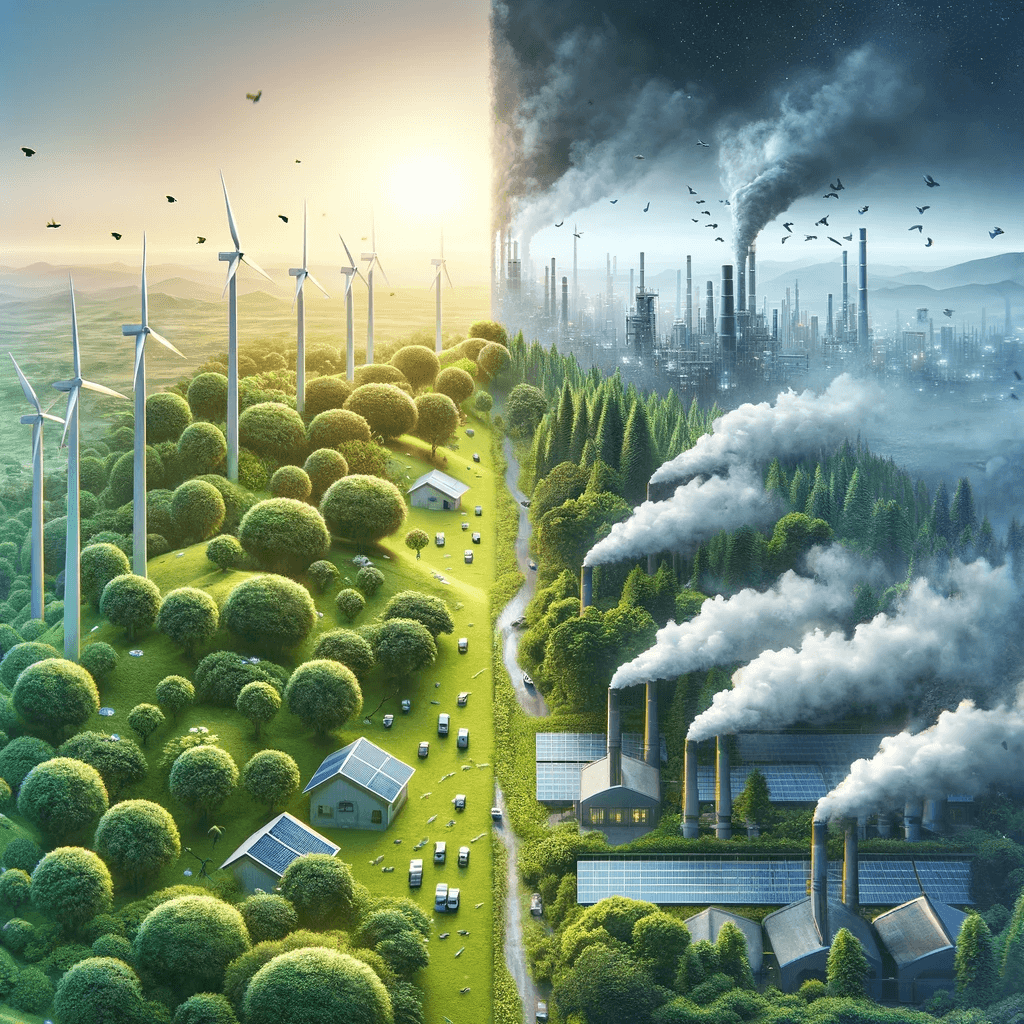
Nations differ in their environmental requirements. New supply chains will require higher standards, and if they are not done right, projects will be stalled as they secure permits.
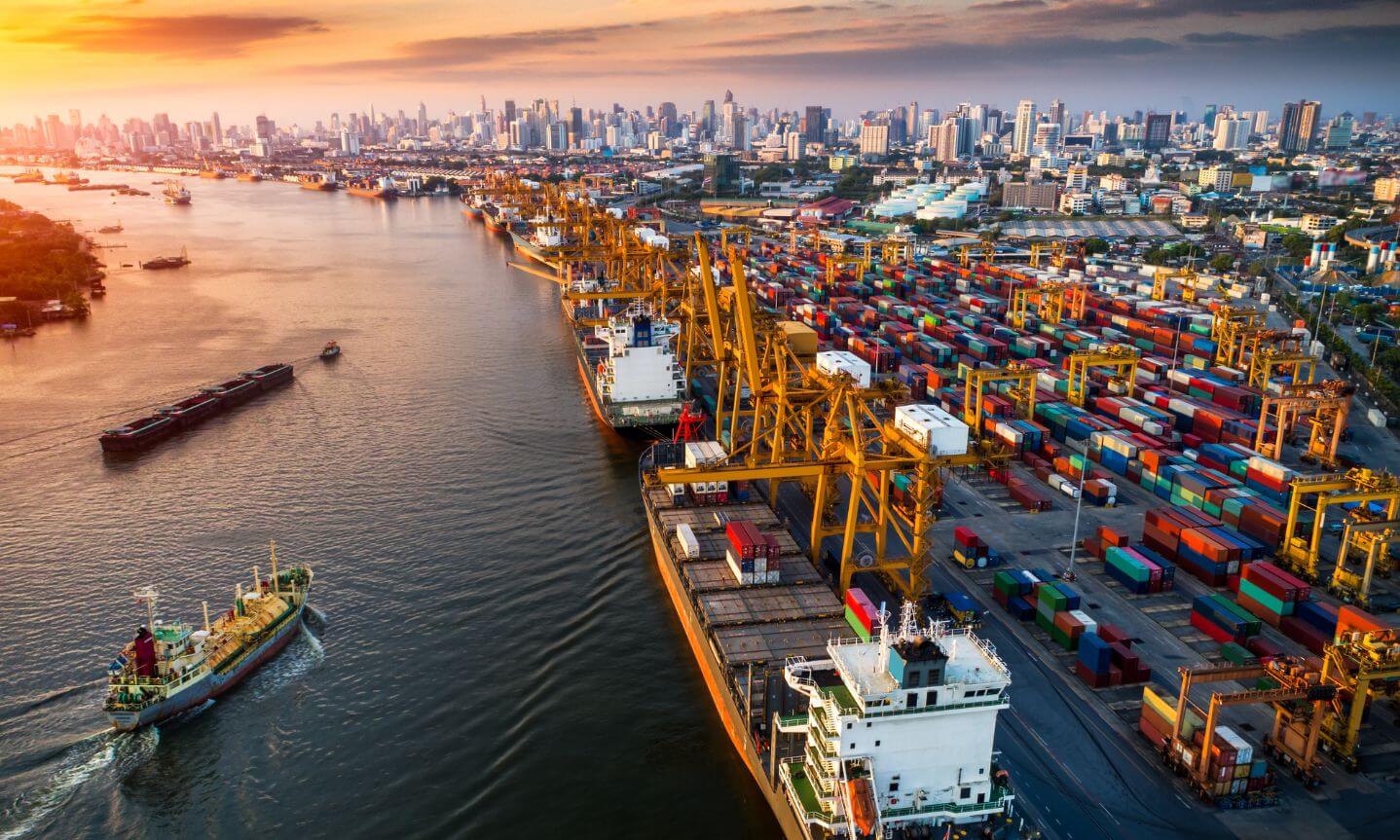
We must address transportation costs and the emissions created along with wasted time.
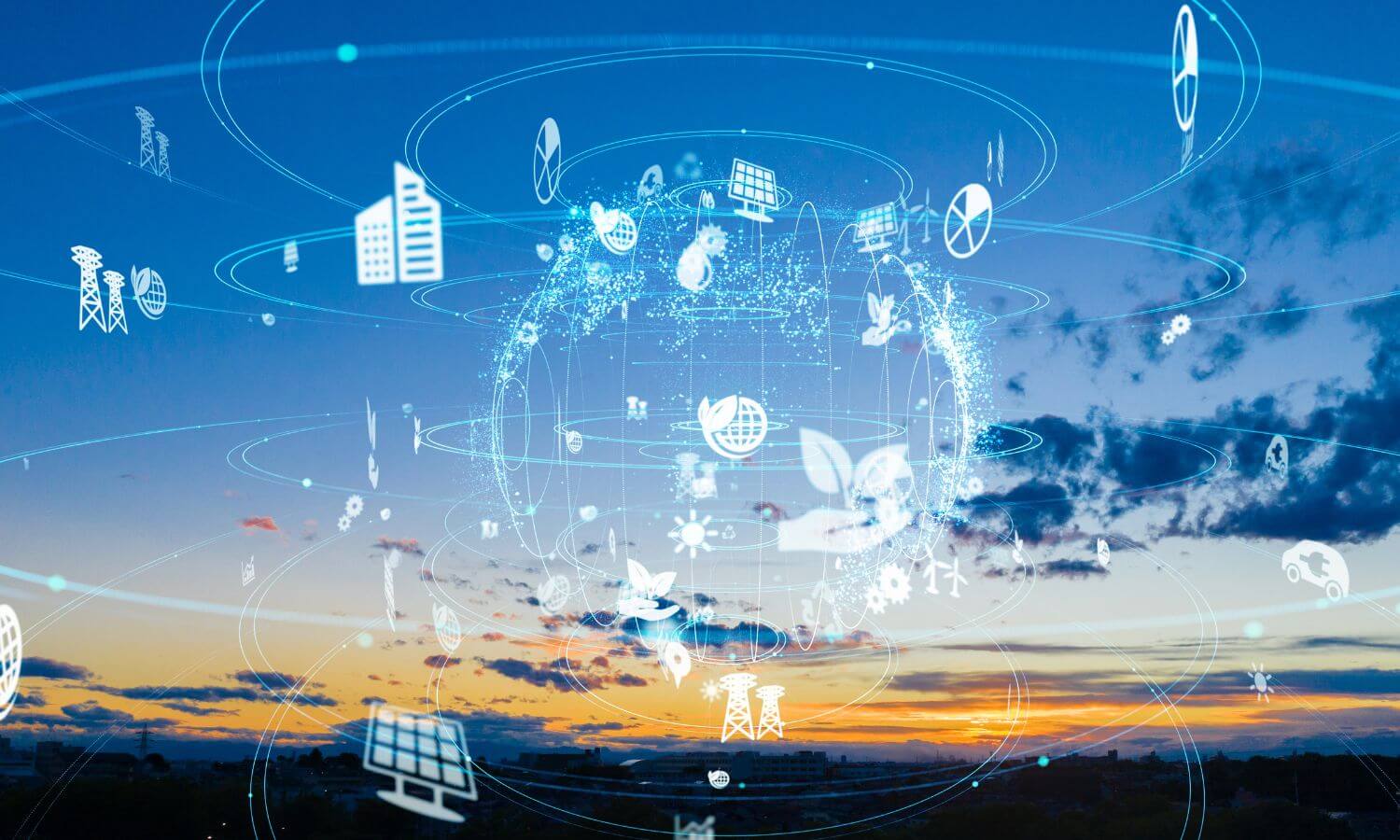
The complex global supply chain is sensitive to disruptions caused by political, economic or natural events.
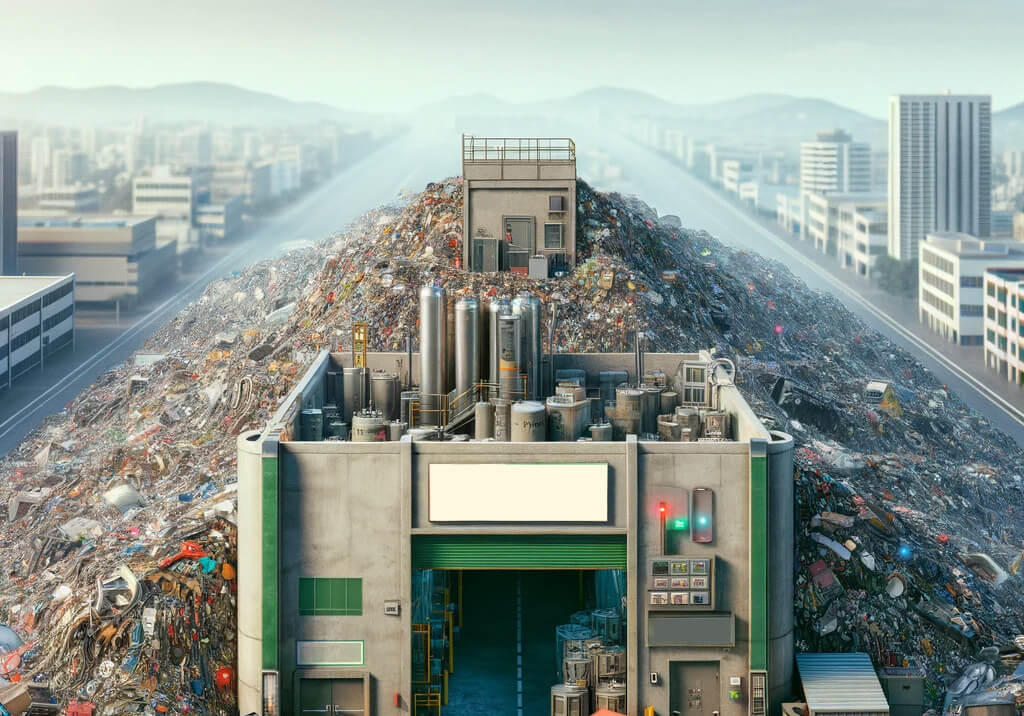
Currently, the recycling infrastructure for cathode materials remains underdeveloped.