Written By: Alex Holmes, Chief Operating Officer at Nano One Materials Corp.
“The EV industry is trying to mobilize 8 billion people with cleaner transport and energy solutions using manufacturing processes and networks designed in the ’90s.”
Lithium-ion batteries—having reliably lit up our phones and laptops for years—are now powering our Electric Vehicles (EVs). Unsurprisingly, the surge in demand has led to a bottleneck in battery metals and chemicals supply chains. That’s because they weren’t designed to fulfill the scale we need to power the energy transition. Despite this, companies are scrambling to ramp up battery production.
Numerous long-term mining projects are underway, preparing to stock these batteries’ future raw material needs. Let’s say they get through all the start-up hurdles and become operational—they still need to catch up to enter a market moving with tremendous pace and momentum. For now, auto OEMs are being pushed by a confluence of factors to adopt different sourcing strategies. Some are investing in mines, and others are investing in recycling.
Supply in operational mines have past and present challenges. Mines are on backorder, and new ones aren’t exactly quick or cheap to build. Nor does the sector have the greatest track record for capital deployment discipline. And while today’s mining sector prioritizes sustainability and community engagement, past practices still haunt it. This makes it a hard place for EV-eager automakers to park their brand. But the reality is that the EV transition isn’t viable without new mines.
A century ago, the auto sector invested in mines to secure the raw materials to build their Internal Combustion Engine (ICE) vehicles. This vertical integration was done out of necessity to alleviate supply chain constraints. Sound familiar? We’re right back to where motorized road transport first began. Direct supply chain investment is a prerequisite today for achieving a successful ICE-to-EV energy transition.
The hard truth about recycling is that we won’t have a sizable amount of EV batteries to recycle until 2030-2040. Yet battery recycling has garnered more attention than sectors in the supply chain with more imminent build-out needs. This is thanks to the widespread understanding of the environmental value associated with recycling. Whether we should source materials from mines or old EV batteries is not in question. We need it all, to be frank. Recycling can become so influential that sector giants like Tesla equate it to the future mines for EV raw materials. Keyword: future.
Zoom Out:
It’s not just raw minerals that are a necessity here. It’s also innovation and collaboration which must continue simultaneously around the supply chain. It is a strategic imperative that we embrace new technology innovations. To adopt a differentiated approach to extracting, refining, processing, and manufacturing critical minerals into battery materials. This will ultimately make recycling more effective when we face the end-of-life for all these batteries. The technology gap that needs to be filled today is in sustainable processes. How do we get there? Embracing change and working together. This is a non-negotiable for a zero-emission, clean energy future.
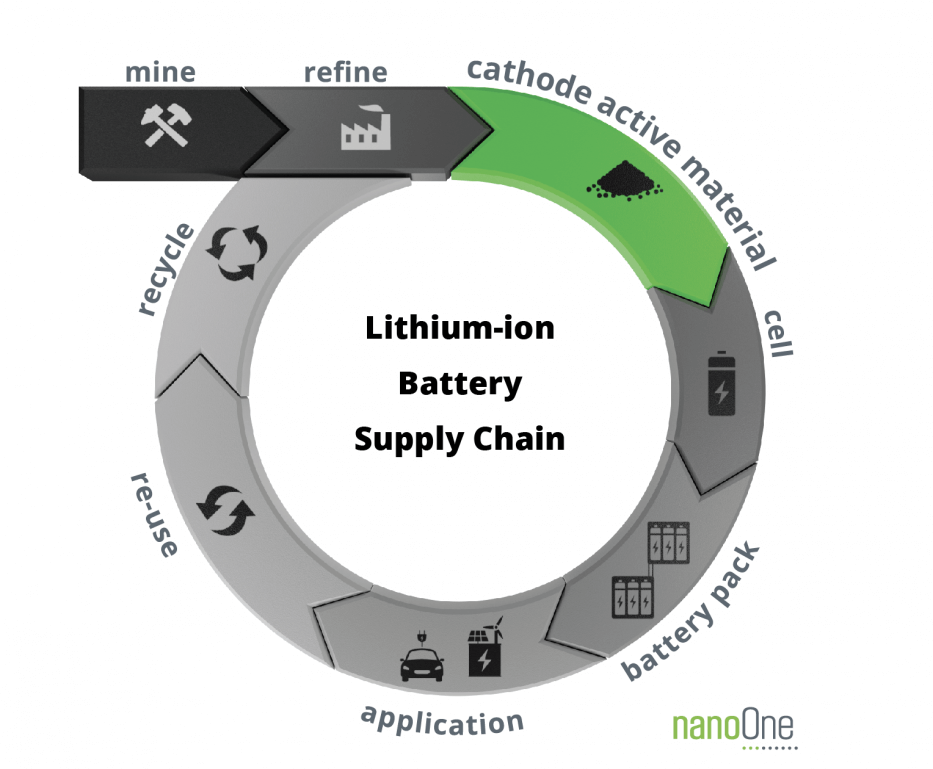
Mining Virgin Raw Materials
“Why not source materials from operational mines? They’ve been spoken for.”
Mines aren’t all at the same stage of readiness, especially in suddenly booming industries like EVs.
Developing a new mine requires a significant upfront investment, with a high risk of not making it past the initial phases. Even if it does, it could take years to produce, meaning it won’t fulfill the short-term sourcing needs. So, why not source materials from operational mines? They’ve been spoken for.
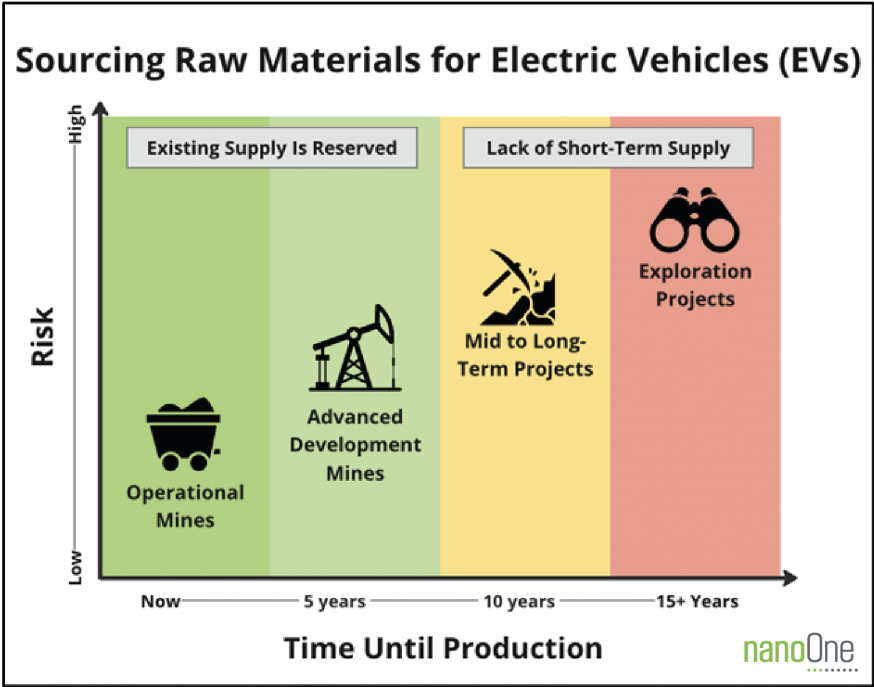
Operational Mines have a supply that is reserved and largely slated to head to China until at least 2025. These mines are the obvious places to go for the pre-requisite materials to supply battery metals and chemicals—the low hanging fruit—but they no longer suffice to meet the projected global demand for EVs.
Advanced Development Mines are about five years away from production (even less if they’re already permitted and financed). The supply here is also largely spoken for—tied up with offtake agreements with the automotive sector today.
Mid to Long-Term Projects aren’t far enough along to secure offtake agreements or an automotive investment using conventional practices. But both are needed to advance these projects closer to becoming mines. They may also be missing key components that mitigate development risk such as asset quality, jurisdiction, “permittability” or a quality senior leadership team. There’s too much risk for the automotives to get meaningfully involved at this stage, which inherently forces these projects to rely on higher cost and often scarce or cyclical risk capital. These projects are five to ten years away from production and require significant funding through many engineering studies while they also navigate permitting and maintain community engagement.
Exploration Projects are even riskier, with the probability of becoming a good development project on the lower side. This isn’t a great place to look for near-term sources anyways, given it could take 15+ years to go from exploration to production.
These are some of the challenges in virgin raw material sourcing that have led to increased investment and short-term material sourcing strategies in recycling.
Recycling Battery Materials
There is no doubt that recycling a battery when it’s no longer useful to the vehicle will play a paramount role in the EV battery material supply chain. Automakers know this, as shown by their willingness to make investments and commitments to ensure that the supply chains of tomorrow are set up properly to support a successful EV transition. These investments appear to be as much about having a recycling plan as they are about making a public statement of support on recycling batteries—a strategy to counter the batteries in landfills narrative. Like the other links in the chain, innovation is critical here to improve efficiency for when there are batteries at scale to recycle.
"Mining for virgin raw materials means it’s coming straight from the earth, for the first time. In contrast, mining for raw materials can also refer to recycling, as minerals are being extracted out of end-of-life batteries."
However, we’re at least 10-15 years away from facing that reality. Possibly longer, given it’s still being determined where batteries go at the end of their useful vehicle life. They may first be re-purposed and go to energy storage applications.
Ultimately automakers will control batteries at their end-of-life— deploying incentives to secure them and send them back upstream—to be the non-mined or, urban mined, source of critical raw materials.
Battery Gigafactories and Scrap Material Recycling
Large-scale battery makers—AKA Gigafactories—produce a considerable amount of scrap materials in their first few years of production. Initial yields are typically less than 50% of total capacity and take years to get to 90% at best. When you hear public discourse on battery recycling today, this is most likely what is being discussed. Some may argue that these aren’t true recycled materials; it’s really waste recovery and is necessary.
Current recycling business models
- In-house Recycling: Some battery manufacturers recycle leftover scrap materials within their production facilities.
- Outsourced Recycling: Battery manufacturers may outsource their recycling processes through external recycling companies.
- Buyer-Trader Model: Battery manufacturers can sell their scrap materials to interested buyers. If the buyer is a recycling company, they can recycle the materials independently or pursue alternative methods.
This scrap ultimately ought to go back into the front end of the automotive supply chain. If not today, it will eventually, because the largest buyers will control their critical minerals.
EV Battery Pack Design Implications on Recycling
Is the customer still always right? I don’t think so. Even consumers need to embrace change to achieve net-zero emission goals. Some quick math reveals that most people don’t need the larger EV.
Yet a prominent challenge in the electric vehicle (EV) industry revolves around the growing demand for larger battery packs to alleviate consumer concerns regarding range limitations. The prevalent desire for 300+ mile electric vehicles stem from auto sector marketers recognizing the need to address customers’ apprehensions regarding daily commutes exceeding this threshold. Understanding consumer behaviour reveals their inclination towards habitual routines, as they prefer not to undergo inconveniences such as altering their charging habits or enduring extended charging times during their presumed 300-mile commutes.
Consequently, the prevailing approach has been integrating larger batteries into the vehicle platform, maximizing kilowatt-hour (kWh) capacity to mitigate range anxiety and drive sales.
These larger battery packs, however, do not typically undergo strenuous usage cycles, given that the average daily or weekly driving distances fall short of the maximum range capacity. Nevertheless, even under more demanding usage scenarios, they are engineered to endure at least 1,000 cycles, specifically for NMC (nickel-manganese-cobalt) batteries. To illustrate, assuming a weekly charging cycle, this translates to nearly 20 years of functional lifespan before the battery capacity falls below 80%—a commonly accepted threshold denoting the end of life for an electric vehicle battery.
Cathode Active Material (CAM) Innovation
Inertia is a powerful force. And its now driving the momentum of the fast-paced build-out of EV battery supply chains which, will arguably only accelerate into the next two decades. But before the rubber really hits the road, we must change how we’re doing things. We must embrace new processes and technologies in every aspect of the supply chain, and CAM manufacturing is no exception.
The current CAM practices are unsustainable and unscalable, particularly if we are to consider them in alignment with the goal to reach net zero emissions by 2050. The CAM manufacturers and automotive players are struggling to put batteries between wheels today. This is common knowledge in the industry. Today’s technology installations are good for the next five, maybe ten years. But to be competitive and to stop a mess before it’s a problem, differentiated technologies will need to be installed.
But commercializing new technology comes with tremendous challenges. Challenges in a sector that is moving with immense momentum. The easy road is to simply repeat. Change is perceived as risky.
There is hope, though. Nano One has a long list of partners willing to change and who see the merits of our technology. They are willing to embrace a challenge. Leaders like Rio Tinto, BASF, Umicore and most recently, Sumitomo Metal Mining.
This energy transition isn’t just about cleaner transport and energy storage. It’s about cleaning up our planet. And a better future. I don’t want to look back over my shoulder in 20 years only to see another mess we’ve created.
I know you don’t either.
Sources
The Economist Podcasts
https://open.spotify.com/episode/5RBZigzWJXvdQAKCrQ0Npw?si=Wj1l4oUIRjaYTxH1TiTJWw&context=spotify%3Ashow%3A12zKAMNyS2GNentUzxq9QN
Benchmark Mineral Intelligence
https://source.benchmarkminerals.com/article/financing-the-battery-arms-race-the-514-billion-cost-of-bridging-the-global-ev-supply-chain-divide
IEA (2022), Global Supply Chains of EV Batteries, IEA, Paris
https://www.iea.org/reports/global-supply-chains-of-ev-batteries, License: CC BY 4.0
Circular Energy Storage Research and Consulting
https://circularenergystorage.com/articles/2022/9/7/a-tsunami-or-a-drop-in-the-ocean-how-to-calculate-the-volumes-of-lithium-ion-batteries-available-for-recycling
Global News
https://globalnews.ca/news/9405696/electric-vehicle-battery-recycling/amp/
Disclaimer:
This update is provided for informational purposes only and is based on the opinions and interpretations of the management of Nano One Materials Corp. (“Nano One” or the “Company”) as of the date these insights are provided. None of the information or analyses presented are intended to form the basis for any investment decision, and no specific recommendations are intended. Accordingly, this does not constitute investment advice or counsel or solicitation for investment in any security. The Company shall not be held responsible for any direct or consequential loss or damage arising from the use of the information provided herein. This includes, but is not limited to, any interpretation, reliance upon, or other use of such information, as well as any inaccuracies, omissions, or typographical errors. The Company does not undertake any obligation to update any that is incorporated by reference herein, except as required by applicable securities laws. Any actions taken as a result of the information provided are solely at your own risk.
Please note that any links provided to third party websites on this platform are for informational purposes only. We do not endorse or take responsibility for the content, accuracy, or any other aspect of these websites. Additionally, we are not liable for any damages or loss arising from the use or access of any third party website linked to from our platform. Users should exercise their own discretion and review the terms of use and privacy policies of any third party website before accessing or interacting with their content.