As seen in Benchmark Magazine. Benchmark sat down with Dan Blondal, CEO of Canadian cathode developer Nano One, to discuss developing LFP cathode production outside of China
Benchmark: Can you explain why there is so much interest now in lithium iron phosphate batteries or LFP?
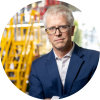
Dan Blondal: LFP is the safest, longest lasting, and lowest cost cathode, but its adoption over the last decade was mostly limited to China, where there were no patent restrictions. It really took off when China stopped incentivising nickel rich NMC cathode alternatives and when LFP battery packs started rivalling NMC on energy density and range. China now makes almost all the world’s LFP, and it is their dominant chemistry for lithium ion batteries. However, the last of the key patents are expiring and LFP is back in the game for North America, Europe and the Indo Pacific region.
Benchmark: What does the Inflation Reduction Act (IRA) mean for LFP and the cathode supply chain? Has it changed your outlook?
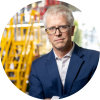
DB: The IRA has had a deep impact on the battery ecosystem across the globe. The injection of US capital and the tax incentives in the IRA are massive and are having ripple effects in Canada, the EU and Asia. It has fast-tracked planning and greenlit some significant projects. And yet, many decisions are on hold while stakeholders—big and small—wait for further clarity and weigh in on the trade-offs and implementation of IRA’s key principles, namely job creation, national security and the environment. However, Nano One set its plans in motion before the IRA was introduced and our outlook remains the same. We believe we can be cost-competitive with overseas players while simultaneously delivering on environmental imperatives, friend-shored supply chains, and the need for rapid deployment. Our one pot process enables this for nickel, manganese and iron rich cathode materials and we see LFP as our nearest-term opportunity, using our Québec facility as our commercial launchpad and the world as our target market.
Benchmark: What makes you think that LFP can be done outside of China?
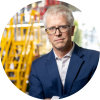
DB: LFP cathode materials can certainly be made in North America and other regions, but they must be cleaner, greener, leaner, and faster. And they must be cheaper. This will require innovation and collaboration.
At Nano One, our one-pot process is a flexible production platform for a wide range of cathode materials, and we are using it to change how LFP is made as well as nickel and manganese-based cathodes, known as NMC and LNMO. It eliminates the waste and greenhouse gases being generated in China, reduces manufacturing complexity, decouples from their supply chains, and most importantly, it is also cost competitive. And by partnering with large and like-minded players, we can establish secure supply chains and design plants that can be licensed to many and quickly scaled to meet the projected demand.
In fact, the first tons of LFP got their start in Canada back in 2005, thanks to the original inventor Dr. Goodenough, further innovations at Hydro Québec and the University of Montreal, and their first licensee— Phostech Lithium—in Candiac, Québec. The Phostech plant came to be owned and operated by Johnson Matthey Battery Materials Canada, which we acquired in 2022 as a launch pad for our one-pot LFP.
Nano One’s Candiac facility is the only LFP plant outside of Asia and it is now being recommissioned for one-pot LFP. The team there has 10-plus years of scale-up and operational experience producing LFP for tier-1 automotive customers. We have permits in place and expansion plans underway to demonstrate at larger scales. Candiac literally accelerated our commercialisation plans by years and gave us a tremendous head start in the race to ramp up LFP.
Benchmark: Canada obviously has a long history in batteries and critical minerals, what is driving this?
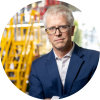
DB: Location, location, location. Canada is fortunate to be the resource-rich and northern neighbour to the United States with a long-standing and robust free trade agreement. The two countries have an integrated automotive supply chain and the U.S. is the largest global economy, rapidly transitioning to clean energy. Canada has access to low-cost, clean, renewable energy with critical minerals in our backyard. We have a highly educated workforce, crucial immigration policies, a framework of responsible mining, and world-class environmental standards. Our government has enviable programs that support companies through early-stage innovation, the dreaded commercialisation gap, project finance, and export development—all while attracting foreign investment.
And we have Québec, which has been investing in the battery ecosystem for longer than anyone but Japan. And Ontario with its well-established and integrated automotive manufacturing sector. And my home province in British Columbia, where a thriving entrepreneurial culture led to the commercialisation of the very first lithium ion batteries and fuel cells, which catalysed world-class academic programs and pioneering researchers from coast to coast.
Benchmark: Cathode production and investments continue to be centred in Asia, particularly China. What are the main challenges for Europe and North America in developing the capacity to support their supply chains?
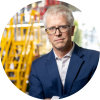
DB: China certainly dominates battery and cathode production and controls a big part of the supply chain that feeds it. Investments there have been very strategic over the last decade, outpacing anywhere else in the world, and affording them considerable dominance across the sector. Nowhere is this more obvious than with LFP batteries, where China controls 99% of the world’s LFP cathodes—representing 60% of their battery market.
It is enormously challenging to emulate this in Europe and North America, where everybody is scrambling to put batteries between wheels and relying on Asian expertise and supply chains. This is playing out while countries try to nurture and implement home-grown battery manufacturing solutions, materials, refining and mining that must eventually compete with supply chains with a 10-year head start. It is obvious that nations must invest trillions like China has, but the heavy lifting and competitive opportunities lie in doing it better, cheaper and with a much lighter environmental footprint. We have the benefit of hindsight, which is the second-mover advantage, but we must streamline resource extraction while embracing technology, its promises, and its risks. We must do so collectively and with purpose, we must be stewards of our environment and our precious resources, and we must do so with a massive scale in mind—scales that will have us thinking like the petrochemical industry. To borrow a wonderful phrase from our partner Rio Tinto—start small, think big, move fast.
Benchmark: Speaking of Rio Tinto, they made a strategic investment in Nano One in 2022 and you added another partnership in 2023 with Michigan-based LFP battery pioneer, Our Next Energy (ONE). How do you view these relationships?
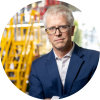
DB: Interestingly, the crux of making LFP is iron. China is the only country with mass amounts of iron sulphate tailings—an industrial by-product—which they use to produce LFP, with many wasteful environmental downsides. By leveraging Canadian-made and readily available class-1 automotive-quality iron-metal powders from our strategic partner, Rio Tinto, we are developing an iron supply chain for LFP that is powered by renewable energy with no wasteful by-products and no wastewater. It is cleaner, cheaper, and we think the fastest route to IRA compliance and 100% North American-made LFP. This is the vision that brought Rio Tinto and Nano One together. Our partnership with Michigan-based Our Next Energy fits neatly into this plan because their A123 origins give them the home-grown development and production experience that America so badly needs. They are developing high energy density, long-range LFP batteries, and our expansion strategies are aligned with theirs in building out the North American market. We will have the Québec plant re-commissioned for one-pot LFP later this year and will begin evaluation and qualification with our partners. We believe this will mitigate supply chain uncertainty, meet localisation imperatives, and enable automotive OEMs and renewable energy storage to meet their net-zero mandates with the wide-scale and rapid adoption of LFP.
Benchmark: Nano One also announced joint development partnerships with Umicore and BASF. What was the purpose of these deals?
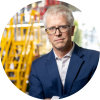
DB: These collaborations are important to us. Our efforts with Umicore and BASF are aimed at making each party’s proprietary formulations of nickel and manganese-based cathode materials using Nano One’s one-pot process. We are aiming to reduce cost, complexity, environmental footprint, and energy intensity and — more so than ever — to leverage local inputs and reduce reliance on uncertain supply chains. Having NMC and LNMO development programs with large global players in the space diversifies our business prospects and demonstrates the flexibility of our one-pot process and the potential for licensing and collaboration. Positive results could lead to piloting, licensing, and commercial production, and we are encouraged by the work that is underway.
Benchmark: At the heart of all this, you always bring it back to reducing waste and complexity. Can you expand on that? Where is most of this occurring and how can this change?
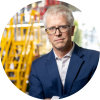
DB: Waste comes in the form of energy, chemicals, water, transportation logistics, and land use. When this industry started on the commercial leg of its journey in the late ‘80s, production volumes were low and the resulting waste was negligible, causing no alarm. However, these processes were not designed with the volumes needed for the net-zero future, a future that will need half a billion tons of cathode capacity. As production lines grow bigger and longer and wider and faster, the volume of materials being shipped, the land-use requirements and the waste being generated will become major impediments to growth, particularly as production shifts to jurisdictions with stricter environmental standards—and therein lies the generational opportunity that Nano One aims to address.
Benchmark: Can you give us a refresher on the basics of battery waste?
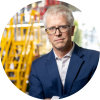
DB: Cathode active materials are made primarily in China, with metal sulphate feedstocks that are chemically processed into mixed metal precursors, known as precursor cathode active material, or PCAM. The need for these metal sulphates and the costly logistics of shipping them is forcing the industry to co locate its refineries and processing facilities with PCAM production, complicating supply chain relationships, limiting where these facilities can be built, and proving to be very difficult to permit.
That’s because the PCAM process generates large amounts of wastewater and sodium sulphate by-product, where the sulphate alone is 3 times larger than the product stream. The waste is even larger when recycling.
While sulphate waste has been traditionally repurposed in detergents, fertilisers and building materials, the excesses of PCAM production will overwhelm these markets. Its solubility prevents it from being landfilled in all but the driest places on earth, and disposal in rivers and oceans is not a scalable option. Recycling sodium sulphate into caustic soda and sulphuric acid is prohibitively costly in terms of CAPEX and energy intensity. This is not aligned with global net-zero ambitions by 2050 and not how we want to use our precious energy resources, land, and water. PCAM is then mixed with lithium carbonate or hydroxide and thermally processed into cathode powders before coatings are applied in a final thermal treatment. The thermal processing is energy intensive, CAPEX heavy and it dominates the physical footprint of the plant. Each furnace is the size of a football field, dozens will be required for each EV battery line and it takes days to cook the materials.
Benchmark: How do Nano One’s processes approach these issues?
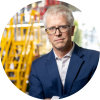
DB: Nano One’s one-pot process is inherently flexible, and it enables cathode to be made from a range of readily available sulphate-free raw material inputs, that are a fifth the shipping weight of sulphates and use a fraction of the water with no sulphate by-product. This eliminates the need to co-locate refineries with cathode production, eases permitting, and enables distributed manufacturing on smaller land packages, providing considerable environmental, economic, security and partnership advantages over incumbent methods.
In the one-pot process, all reactants—lithium and coating materials included—are combined in a single reactor at ambient temperature and pressure and allowed to react. The resulting slurry is dried, and because it is already lithiated, it can be thermally processed quickly using smaller, more efficient and more productive furnaces. The simplicity of the one-pot enables lower CAPEX and OPEX by eliminating process steps, wastewater handling and the generation of all sulphate waste. Coatings also form simultaneously with single-crystal structures for improved durability and a smaller environmental footprint.
One-pot enables cathode production from various battery metal feedstocks, including directly from class-1 sulfate-free metal powders such as iron and nickel — and lithium inputs can be in the form of carbonate or hydroxide. This flexibility enables a more localised supply and eliminates the need for upstream conversions of metals to metal sulfates and lithium carbonate to lithium hydroxide, reducing the required infrastructure investment, logistics and the associated GHGs.
Benchmark: Lastly, there is talk of solid-state batteries, sodium ion batteries and other measures that will replace traditional lithium ion batteries. Is Nano One working on next-gen battery materials?
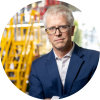
DB: These technologies are very much needed, and we welcome them all, but they will not replace lithium ion batteries. Rather, they will address a wider and wider set of energy storage needs, complementing and hopefully easing the global burden on lithium ion and its supply chains. We have a proven track record of recognizing and leading long term battery material trends and our teams, in B.C. and Québec, are continually collaborating and innovating to reduce waste, emissions, complexity and cost by transforming the processes and the supply chains so they can be scaled and made sustainable for the net-zero future.
Disclaimer:
This interview is being provided for informational purposes only and is based on the opinions and interpretations of the management of Nano One Materials Corp. (“Nano One” or the “Company”) as of the date these insights are provided. None of the information or analyses presented are intended to form the basis for any investment decision, and no specific recommendations are intended. Accordingly, this does not constitute investment advice or counsel or solicitation for investment in any security. This interview may contain forward-looking statements and cannot be a guarantee of future results or events. Forward-looking statements are subject to known and unknown risks, uncertainties and other factors that may cause the actual results, performance or achievements of the Company or its technologies and the benefits therefrom, or the anticipated global market demand to be materially different from those expressed or implied by such forward-looking statements. The Company shall not be held responsible for any direct or consequential loss or damage arising from the use of the information provided herein. This includes, but is not limited to, any interpretation, reliance upon, or other use of such information, as well as any inaccuracies, omissions, or typographical errors. The Company does not undertake any obligation to update any forward-looking statements that are incorporated by reference herein, except as required by applicable securities laws. Any actions taken as a result of the information provided here are solely at your own risk.
Article posted with permission from Benchmark Mineral Intelligence from their “Benchmark Magazine Q2 Review 2023” edition. For more visit: www.benchmarkminerals.com.
Links provided to third party websites are for informational purposes only. We do not endorse or take responsibility for the content, accuracy, or any other aspect of these websites. Additionally, we are not liable for any damages or loss arising from the use or access of any third-party website linked to from our platform. Users should exercise their own discretion and review the terms of use and privacy policies of any third-party website before accessing or interacting with their content.